Efficient forklift fleet management is crucial for businesses aiming to maximize productivity and reduce operational costs. By optimizing how forklifts are utilized, leveraging data for informed decisions, enhancing operator training, and implementing regular maintenance schedules, companies can significantly improve their overall efficiency. This article provides comprehensive tips and strategies to help businesses optimize their forklift fleet management effectively.
Key Takeaways
- Analyze your operational requirements to determine the appropriate number of forklifts needed for maximum efficiency.
- Utilize comprehensive fleet data to make informed decisions and optimize fleet management.
- Enhance productivity by developing and implementing effective operator training programs.
- Implement regular maintenance schedules to ensure forklifts operate at peak performance and reduce unexpected breakdowns.
- Optimize facility layout and forklift routing to minimize travel distances and improve overall efficiency.
Optimizing Fleet Utilization for Maximum Efficiency
Optimizing fleet utilization is essential for improving efficiency and reducing unnecessary expenses. By closely monitoring usage patterns, you can identify opportunities to redistribute or retire underutilized forklifts.
Leveraging Data for Informed Fleet Management
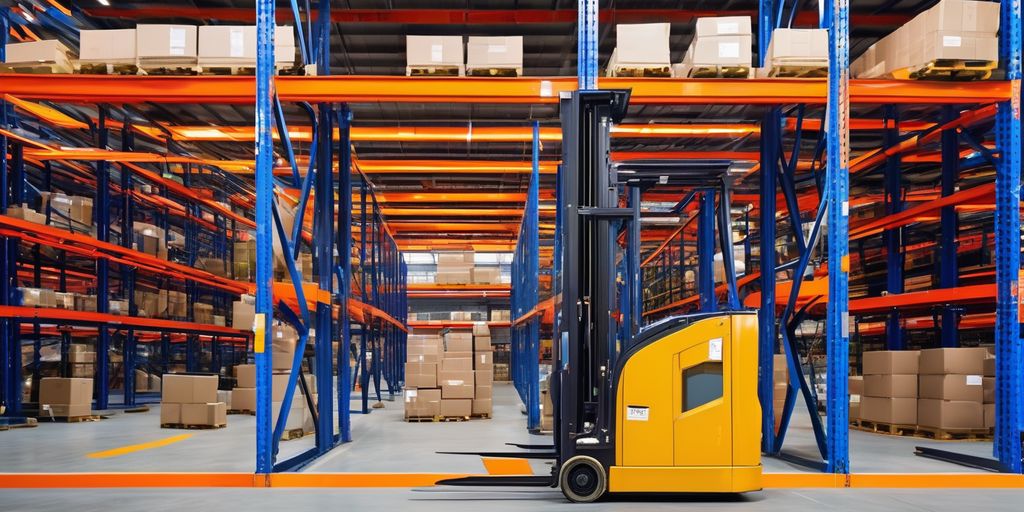
Gathering Comprehensive Fleet Data
Effective forklift fleet management involves gathering, analyzing, and leveraging relevant fleet data to reduce expenses while improving productivity for both operators and vehicles. Access to comprehensive information brings new insights into fleet operations and helps answer critical questions, such as:
- What are the most common causes of downtime?
- How can we optimize maintenance schedules?
- Which forklifts are underutilized?
Analyzing Key Metrics
Data collection is key to optimizing fleet utilization and making informed purchasing decisions. Although specific metrics will vary based on fleet composition, here are some data points most every fleet manager will want to monitor:
Metric | Description |
---|---|
Utilization Rate | Percentage of time forklifts are in use |
Downtime | Amount of time forklifts are out of service |
Maintenance Costs | Expenses related to upkeep and repairs |
Fuel/Energy Consumption | Amount of fuel or energy used |
When this data is aggregated across your entire forklift fleet, it provides a holistic view of fleet operations. That said, simply collecting data isn’t sufficient. It's crucial that this data is consolidated and presented in a format that aids decision-makers without overwhelming them.
Implementing Data-Driven Decisions
By understanding the needs of your fleet and analyzing potential cost savings, you can make informed decisions about how to best manage and maintain your fleet. This can help you maximize the efficiency and cost savings of your fleet. Additionally, a comprehensive analysis can help ensure safety and compliance, helping to reduce the risk of accidents and injuries.
Leveraging data for decision making is essential for mastering truck fleet management. Utilize the data collected from fleet management software to make informed decisions. Analyzing trends in fleet data can lead to significant improvements in efficiency and cost savings.
Tracking, and other data sources, give a holistic view of the fleet's performance. This approach not only optimizes scheduling but also drives efficiency and safety in warehouses.
Enhancing Productivity Through Operator Training
Proper training is crucial for maximizing the efficiency and safety of forklift operations. Operators who know how to use equipment properly make fewer mistakes and are more likely to take care of equipment, extending its operational life.
Implementing Regular Maintenance Schedules
Benefits of Scheduled Maintenance
Regular maintenance prevents breakdowns, enhances efficiency, and ensures compliance with safety standards. Scheduled maintenance is more cost-effective over time, mitigating potential issues and maintaining overall vehicle health. A proactive maintenance schedule includes regular servicing and prompt repairs to address any issues that may arise.
Creating a Maintenance Plan
- Adhere to the manufacturer’s recommended maintenance schedule.
- Conduct essential repairs immediately.
- Consider a maintenance contract with a forklift service firm for large fleets.
- Monitor scheduled and unscheduled repairs, noting work performed, maintenance dates, parts used, and associated labor costs.
Monitoring Maintenance Effectiveness
To ensure the effectiveness of your maintenance plan, keep accurate records of all maintenance activities. This includes:
- Maintenance dates
- Parts used
- Associated labor costs
Vehicle replacements can be based on real-world servicing costs, not estimates, with the assurance that all lifts receive consistent, thorough maintenance.
A preventative maintenance checklist for forklifts ensures thorough assessment and documentation for compliance. Operator training is crucial for safety.
Optimizing Facility Layout for Better Forklift Operations
Optimizing your facility layout is crucial for enhancing forklift operations. A well-designed layout can significantly reduce travel time and increase productivity. Here are some key strategies to consider:
Designing Efficient Layouts
One of the most effective ways to make your facility more efficient is to reorganize it. It’s a short-term inconvenience, but you’ll enjoy significant long-term productivity gains. When forklift operators have to go back and forth across your facility to fill one order, that’s an efficiency killer - death by a thousand cuts.
Minimizing Forklift Travel Distance
Arrange products for optimum efficiency. This also minimizes total forklift miles. Get an inside track on your volume, and warehouse optimization is easier than you think!
Utilizing Telematics for Layout Optimization
If your forklift has a telematic device, the data can tell you how much time your operators spend just driving around. If you don’t use telematics, or if you’d like some expert help digging through the numbers, let us know. Mid-Columbia Forklift and MidCo Material Handling provides free warehouse optimization consultations.
Layout optimization doesn't have to mean reorganizing your entire workplace. It could be as simple as arranging products more efficiently to minimize travel distances.
Adopting Best Practices for Forklift Routing
Analyzing work schedules is crucial for optimizing forklift routing. By understanding peak operation times and aligning forklift availability accordingly, businesses can ensure that their forklift operators are always ready when needed. This reduces idle time and maximizes productivity.
Optimizing load sizes involves balancing the weight and volume of loads to ensure forklifts operate efficiently. Overloading can lead to increased wear and tear, while underloading results in unnecessary trips. Striking the right balance is key to maintaining optimal performance and reducing operational costs.
Reducing travel distances within the warehouse can significantly enhance efficiency. By strategically placing high-turnover items closer to shipping areas and arranging products for optimum efficiency, businesses can minimize total forklift miles. This not only saves time but also reduces fuel consumption and wear on the equipment.
Efficient space utilization techniques using forklifts can greatly improve warehouse operations. By examining aisle widths and increasing storage density, businesses can further optimize their layouts for better forklift operations.
Achieving Cost Savings Through Strategic Forklift Management
Identifying Cost-Saving Opportunities
To achieve cost savings, businesses must first identify areas where expenses can be reduced without compromising efficiency. A comprehensive forklift analysis can provide invaluable insights into how to best manage and maintain your fleet. Key areas to consider include:
- Maintenance costs
- Fuel consumption
- Operator efficiency
Implementing Cost-Effective Strategies
Once cost-saving opportunities are identified, the next step is to implement strategies that address these areas. Proactively managing forklift usage can help extend the lifespan of equipment and minimize repair expenses. Efficiently scheduling forklift operations can also help reduce fuel consumption and overall operating costs.
Measuring Financial Impact
To ensure that the implemented strategies are effective, it is crucial to measure their financial impact. This can be done by tracking key metrics such as maintenance costs, fuel consumption, and operator productivity. Regularly reviewing these metrics will help businesses make informed decisions and adjust strategies as needed.
By optimizing forklift usage, businesses can achieve several cost-saving benefits, including reduced maintenance costs and lower fuel consumption.
Conclusion
In conclusion, optimizing forklift fleet management is a multifaceted approach that requires careful analysis and strategic implementation. By leveraging comprehensive data, businesses can gain valuable insights into their fleet operations, enabling them to make informed decisions that enhance efficiency and reduce costs. Key strategies include efficient fleet utilization, regular maintenance, operator training, and optimized routing. By focusing on these areas, businesses can not only improve productivity but also achieve significant cost savings. Ultimately, the goal is to create a streamlined and efficient forklift fleet that supports the overall operational objectives of the organization.
Frequently Asked Questions
How can I determine the appropriate number of forklifts for my operations?
Analyze your operational requirements to determine the appropriate number of forklifts you need. By closely monitoring usage patterns, you can identify opportunities to redistribute or retire underutilized forklifts.
What are the benefits of gathering comprehensive fleet data?
Gathering comprehensive fleet data allows you to gain new insights into fleet operations, reduce expenses, and improve productivity for both operators and vehicles.
Why is operator training important for forklift fleet management?
Proper training significantly impacts forklift efficiency and safety. Well-trained operators are more productive and can handle forklifts more effectively, reducing the risk of accidents and equipment damage.
How does scheduled maintenance benefit forklift operations?
Scheduled maintenance helps prevent unexpected breakdowns and ensures that forklifts operate at peak performance levels. This leads to improved efficiency and reduced downtime.
What strategies can be used to optimize facility layout for better forklift operations?
Designing efficient layouts, minimizing forklift travel distance, and utilizing telematics for layout optimization are key strategies to enhance forklift operations within a facility.
How can businesses achieve cost savings through forklift optimization?
By identifying cost-saving opportunities, implementing cost-effective strategies, and measuring financial impact, businesses can achieve significant cost savings through strategic forklift management.
Leave a comment
This site is protected by hCaptcha and the hCaptcha Privacy Policy and Terms of Service apply.